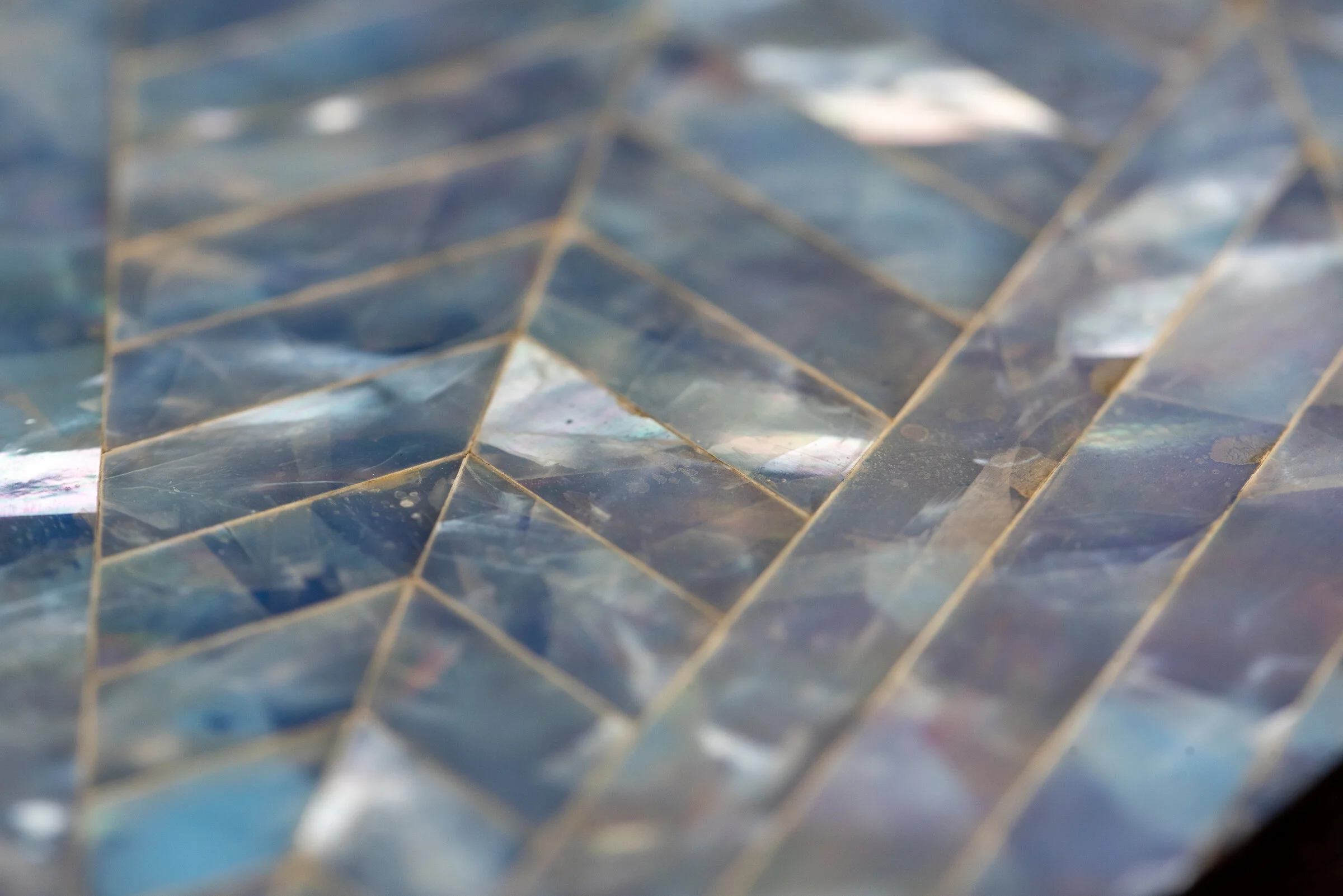
Commissioning Marquetry
The Brief
Working with Aryma is a creative, collaborative and thoughtfully managed process dedicated to achieving the highest standards from concept to completion.
The starting point is the time our design team invests to fully understand the client’s own requirements and aspirations for the project. Every member of our team is both a fine artist and a trained marqueteur, so one person will oversee a project from origination of concept artwork to placing the final piece of veneer.
“It is hard to realize that such skillfully made inlaid woodwork is possible today – but it is and it rivals the quality of marquetry from any age.”
— Rodney Black Design Studios —
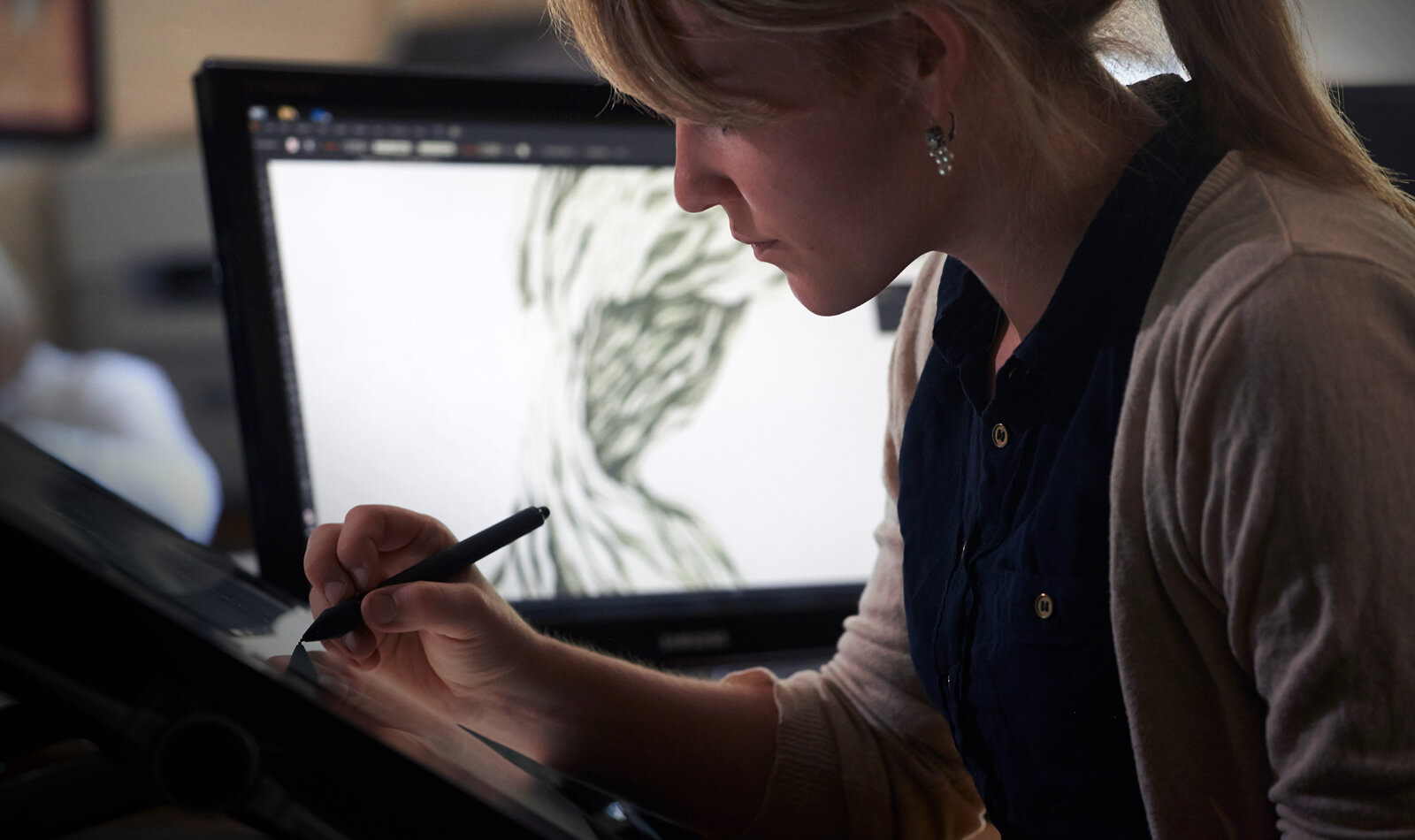
Concept Development
The marqueteur begins by hand-drawing ideas inspired by the brief, evolving these over several weeks with the use of cad into detailed depictions of the proposed design. These are then presented with swatches of sample veneer and other inlay materials, and the client is invited to suggest changes that are then incorporated into the final, agreed design.
Materials
Over the past ten years, Aryma has built up an extensive library of veneers and is able to offer an unrivalled level of experience and knowledge in this field. The greatest care is taken to choose veneer of the highest quality and consistency, whether from familiar timbers such as oak, walnut or sycamore, or rarities and exotics including amboyna and madrona.
Each leaf of veneer is as individual and beautiful as the tree it came from, providing a rainbow palette of colours, grain patterns, figures, burrs and natural features from which our marqueteurs can create the effect they want. In addition, our designs may also incorporate shells and materials, including mother-of-pearl, silver nickel, gold, copper and brass.

Craftsmanship
A single design may comprise many thousands of unique pieces of carefully selected veneer. each piece undergoes four separate processes of cutting, hot-sand shading, pressing and double-cutting before being placed with painstaking precision by the hand of the marqueteur. It takes weeks to assemble a finished piece of work in this way.
Sand shading is a technique that goes back hundreds of years, whereby the veneer is dipped into sand that is heated to 550 degrees, scorching and darkening the wood to give the impression of depth and shadow. It takes great skill and is a time-consuming task that depends for its success on the eye and judgement of the marqueteur.
Finishing
Marqueteurs work in reverse, placing each piece down onto a sticky film backing. Only when it is complete, can the marquetry be turned over and the finished piece seen with all its fine detailing.
This overlay is then pressed onto the appropriate surface, compressing and locking the individual pieces together. This creates a stable and strong surface for final sanding and lacquering. Finishes build up protective layers that enhance the colour and richness of the veneer, while special applications are prepared for aviation, automotive and marine environments.
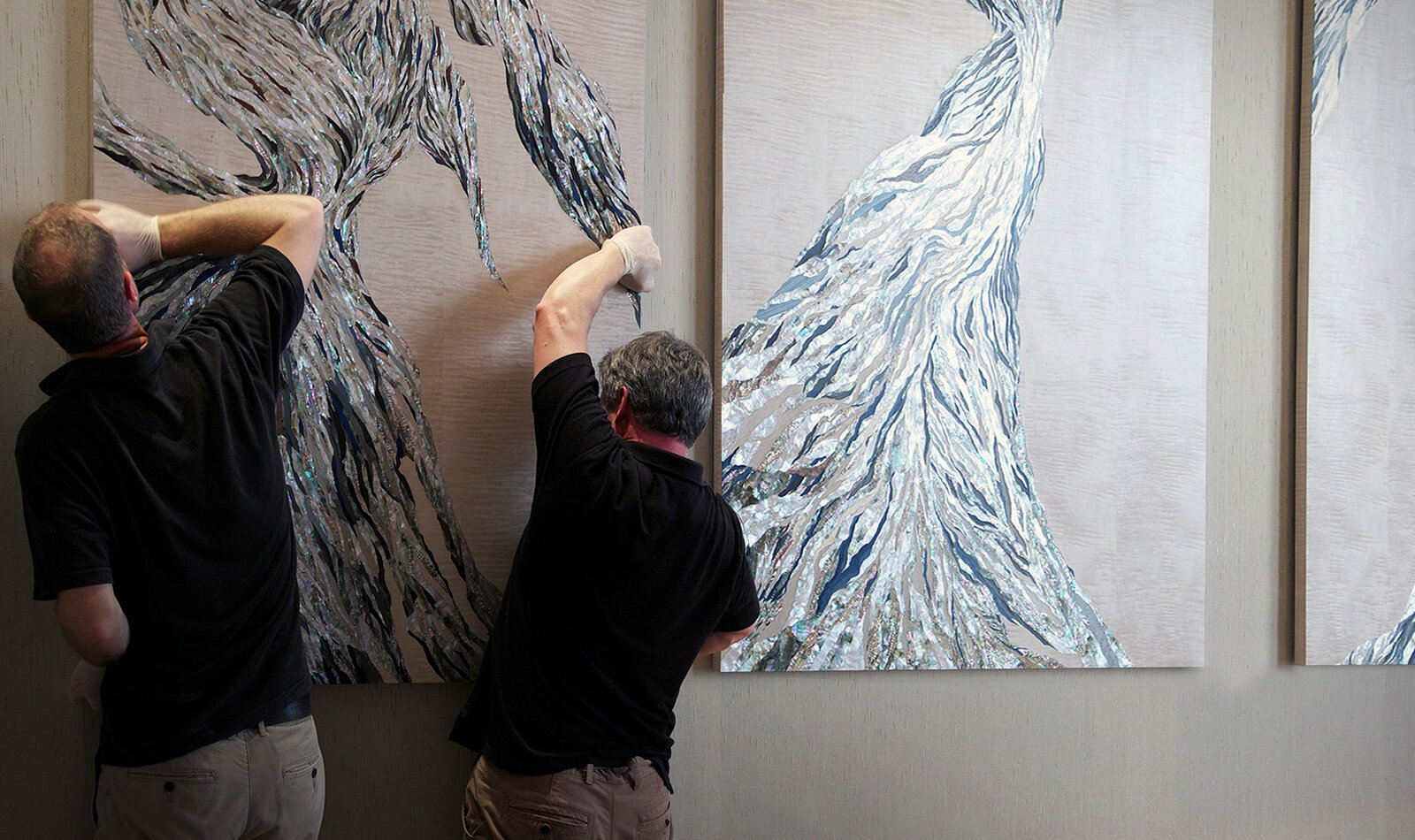
Installation
The final installation depends on the type of project. For furniture and artwork in private residences, for example, our own team will install the finished piece. For marquetry that is an integral part of an interior’s cabinetry or automotive clients, we hand over to the relevant specialist teams.
In either scenario, the entire process is managed seamlessly from our side, ensuring the highest standards of quality and execution.